VisEra is committed to achieving zero safety accidents, building the best healthy workplace, and becoming a worldclass company for ensuring safety and health. We also cultivate a safety culture based on humanistic values and build an intrinsically safe work environment. To ensure safety and security, we support the physical and mental health of employees to achieve work-life balance and we work together with stakeholders to reduce workplace safety and health risks. There were no litigation involving violations of employee health and safety in 2023.
6.4.1 Build a Human-Centric Safe Workplace
Operations of the occupational safety and health organization and system
VisEra has established the Occupational Safety and Health Committee with 56 members (including department heads, engineers and technical staff involved in occupational safety and health, laborers, and managers of occupational safety and health) jointly review occupational safety and health issues to transform the Company into a benchmark for occupational safety and health. Non-management personnel account for 57% of the members. The Committee also convenes meetings regularly each month, which exceeds regulatory requirements and facilitates full consultation and communication for all employees. We established the employee proposal system to strengthen employee consultation, participation, and communication. Employees can file proposal forms or provide feedback to the Occupational Safety and Health Committee.
The Company according to the Occupational Safety and Health Management Regulations continues to obtain certification by independent third-party certification institutions for the ISO 45001/TOSHMS Occupational Health and Safety Management System to continue to improve safety and health in the work environment (Just the Hsinchu and Longtan factories need to apply for TOSHMS, as the Zhongli factory's workforce does not match the necessary conditions). The certification covers 100% of all workers and related routine and non-routine activities in the locations of operations. VisEra has appointed occupational safety and health management personnel (9 in Hsinchu Plant, 1 in Zhongli Plant and 2 in Lonatan as required by law) in accordance with regulations. We also set up dedicated units to help all plants implement regular annual assessments, internal audits, management review, and other matters required by the system. The results pass external certification to ensure their effectiveness and implementation. We also set a target for filing 10 occupational safety management proposals each quarter and 47 proposals were filed in 2023 (the resources invested totaled NT$3.19 million). included automated measuring of photoresist thickness lowers ergonomic risks and prevent musculoskeletal injuries when employees work.
The Company received recognition for the performance of the safety and health management system and was shortlisted by the Hsinchu Science Park Bureau, National Science and Technology Council (hereinafter referred to as Hsinchu Science Park Bureau) as a company with outstanding performance in promoting occupational safety and health in 2023. VisEra employees have won the Occupational Safety and Health Excellent Employee Award presented by Hsinchu Science Park Bureau each year from 2019 to 2023. In 2023, We are humbled to have received National Occupational Safety and Health Awards and OSHA’s outstanding performance awards.
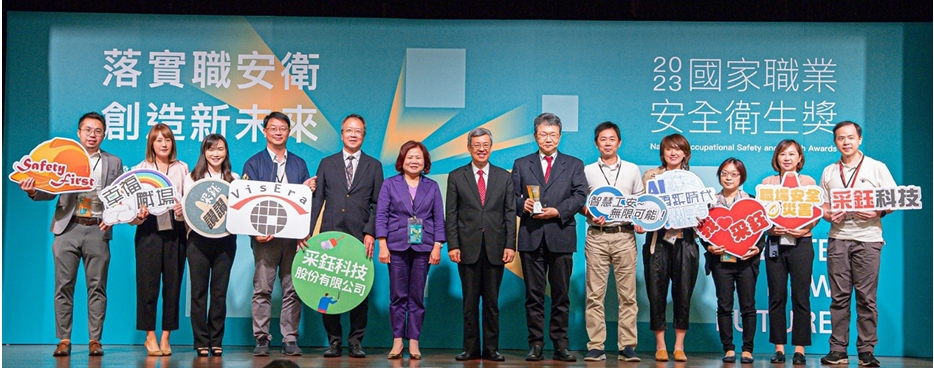
To enhance safety management, we use the audit system to progressively and continuously improve safety management. We conduct regular and ad hoc audits, including daily construction inspections by safety and environmental protection units, weekly routine and project inspections by the safety and environmental department to review the implementation of occupational safety and health management in each plant. We require the responsible unit to propose corrective measures for any failure to meet expectations or violations of regulations. We also set up safety performance indicators (including active and passive indicators) and regularly track the effectiveness of the implementation in each plant every month. The parent company (TSMC) conducts at least 3 audits each year.
We use the system to track all non-compliances or violations found in audits and regularly submit results for review to continuously improve and manage the system operations. Non-compliances are also reported to the Occupational Safety and Health Committee to review the effectiveness of improvements.
Safety Performance Indicators
VisEra has established procedures based on the Occupational Safety and Health Act, domestic and overseas safety and health standards, and ISO 45001 requirements.
To implement the safety and health related procedures, VisEra has established the Safety Performance Index (SPI) system based on the management model of the parent company TSMC to implement quantitative management and supervision of the daily safety and health implementation results in the plants. The SPI includes active and passive indicators and management mechanisms with four color-coded indicators including blue, green, yellow, and red. The indicators have been maintained at blue or green (indicating excellent or good performance).
Description:
●Blue (excellent)-SPI ≧ 95
●green (good)-85 ≦ SPI<95
●yellow (warning)-70 ≦ SPI<85
●red (warning)SPI<70
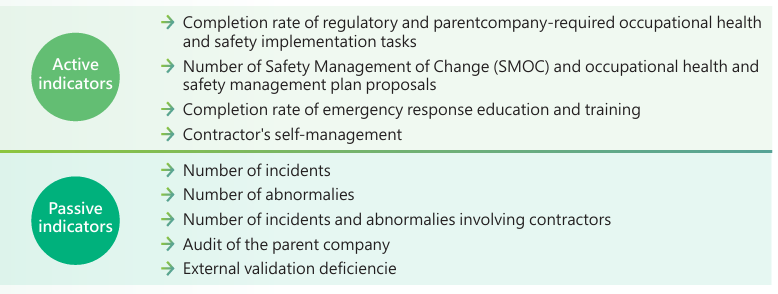
Risk control and opportunities for improvement
VisEra focuses on global safety and health issues, assesses risks and opportunities, and invites employees or representatives in the Company to participate and provide opinions for building a good workplace environment. We set environmental safety and health factors for consideration and hazard identification management procedures, and implement regular evaluations of internal and external issues and issues of concern to stakeholders every year. We determine risk assessments and response to opportunities by considering regulatory compliance, level of concern, technical, financial (including annual operating costs), operational (including operational and business impact on quality, cost, and delivery), and business factors to continuously reduce potential risks. In 2023, we performed 2,681 environmental consideration/risk assessments and evaluations, and assessed 15 internal and external issues and 16 stakeholder requirements and expectations.
We also strengthened the safety awareness of all employees by incorporating the "right to active avoidance of danger" in the Occupational Safety and Health Act so that the concept of safety first can be implemented in the workplace.
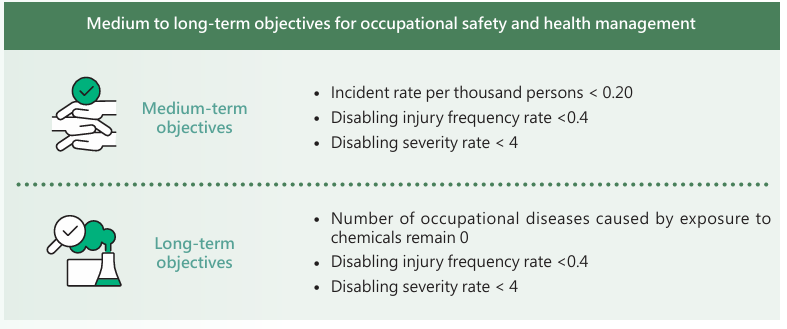
Hazard identification and risk assessment results
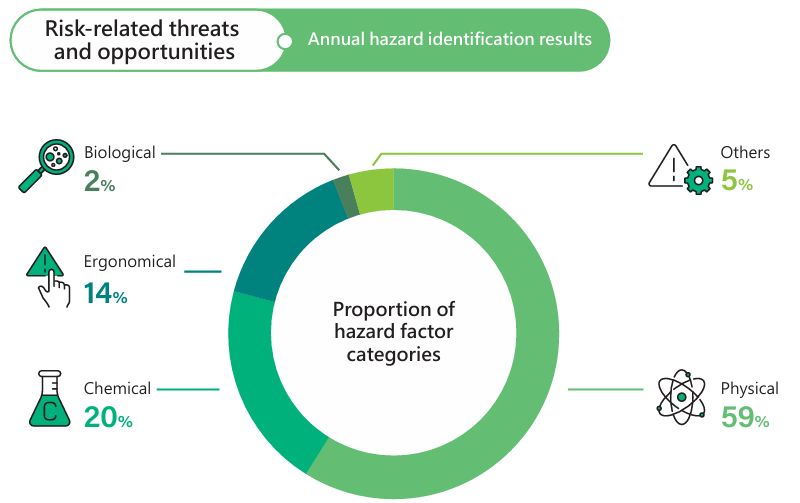
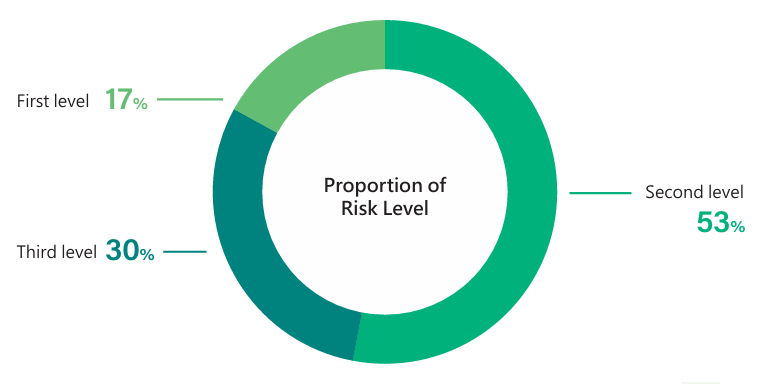
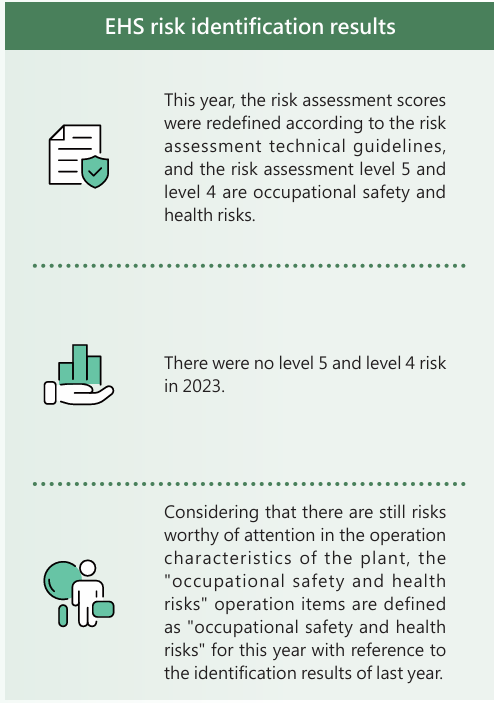
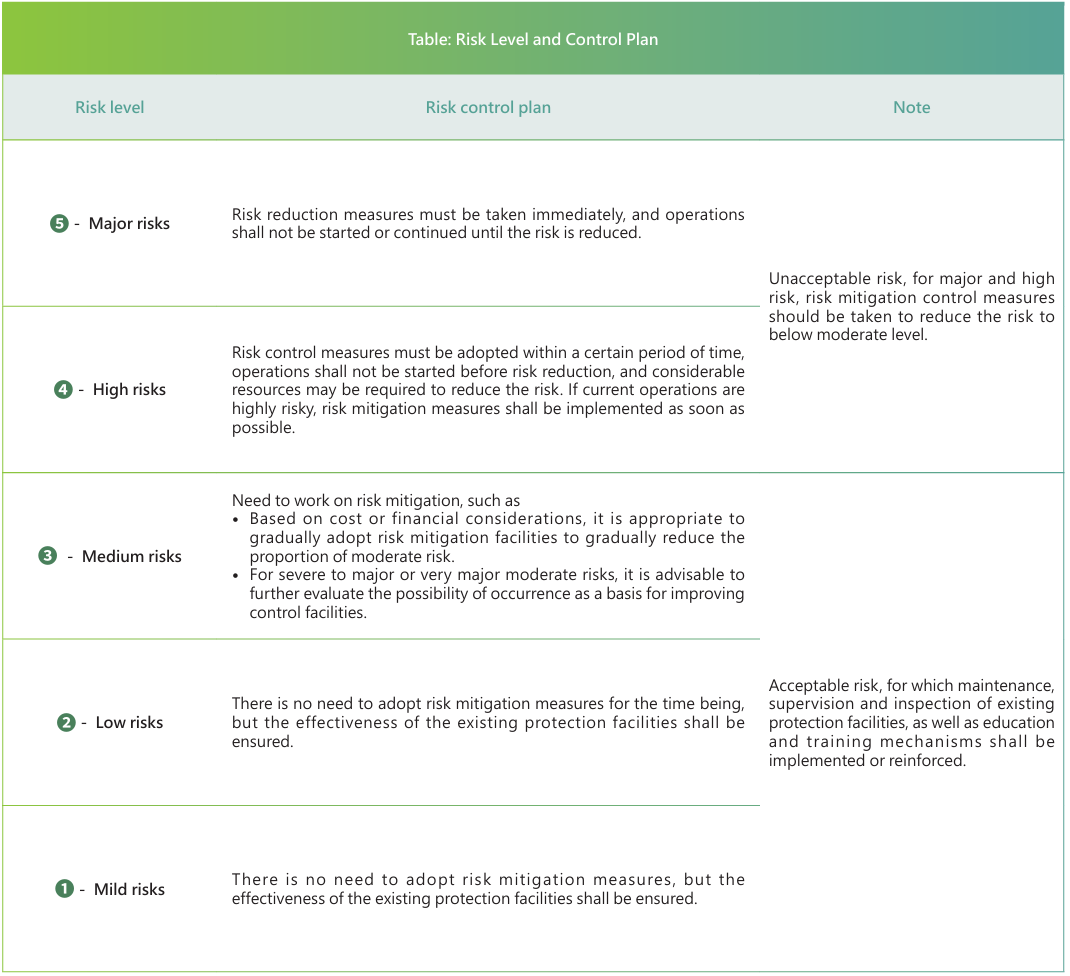
Ergonomic
Continuous actions
• Appoint professional medical specialists to conduct onsite visits and provide recommendations.
• Continue to observe operations and identify potential ergonomic hazard factors in the workplace based on the risk identification methodology and ergonomic hazard assessment tools, and implement corresponding preventive actions.
• Use the Health Center's ergonomic factors questionnaires and records on the use of pain relief patches to monitor employees with musculoskeletal pain. Work with occupational medicine specialists for on-site services and interviews.
Results
• Ask experts in occupational medicine to evaluate the risks associated with the design and operation of mother protection zones in clean rooms and manufacturing facilities. Three recommendations for improving human factors engineering were offered in total; these included enhancing the way that wafer boxes are handled and the light sources used for mask inspection. Improvements have been made to height adjustment, cargo placement height constraints, etc., with a 100% completion rate.
• 1,407 employees completed the musculoskeletal symptom survey questionnaire, and the Company assisted 20 employees with suspected ergonomic risks to attend work interviews and assessments, and arranged onsite visits by occupational medicine specialists to provide recommendations.
• After interviewing employees affected by soreness and pain and identifying the ergonomic risks, we found that they did not work in areas with potential or existing ergonomic risks.
Results
Continuous actions
- In terms of the selection of chemicals, we referenced the green procurement questionnaire of VisEra to process chemicals restricted by the EU REACH regulation. The unit using the chemicals evaluate the feasibility of alternatives and prioritize the selection of chemicals withlow health hazards.
- If chemicals contain CMR substances, IARC substances or The Ministry of Labor's Occupational Cancer Prevention Blueprint has a list of chemicals that should be avoided, don't use it if we are unable to utilize it. Give the selection of compounds with low health hazards top priority. Before utilizing it, we must, if necessary, get the director of the appropriate unit organization's authorization.
- If chemicals contain CMR substances or IARC substances, employees in maternity health protection programs may not engage in related operations.
- Regarding the handling of particular chemical substances, these regulations will be integrated into the environmental, safety, and health procurement specifications to verify whether they comply with regulatory requirements throughout the procurement process. This is because of the new requirements for local exhaust devices in the "Hazard Prevention Standards for Specific Chemical Substances" regulations. criteria for supervision to stop illicit activity.
Results
- The European Chemicals Agency (ECHA) plans to restrict the use of PFHxA by 2035 and VisEra has established related chemical replacement programs for continuous verification and replacement.
- The number of occupational diseases caused by exposure to chemicals remained 0.
Biological
We readily monitor changes in the policies announced by the Centers for Disease Control for continuous adjustments of plant response measures and to provide timely health education information
Continuous actions
- We continue to pay close attention to the development of infectious diseases in Taiwan and overseas. We established preparation and response measures for notifiable diseases.
- We continue to implement reporting mechanisms for non-notifiable diseases and provide health education information for seasonal influenza and dengue fever.
Results
- Support COVID-19 control measures and implement individual epidemic prevention management for high-risk personnel. 0 cases of infections of employees due to business operations. (As announced by the CECC, COVID-19 will be downgraded to Category 4 communicable disease on May 1, 2023.)
Physical
Continuous actions
- Establish a radiation personnel exposure management system :
- Supervision of employees donning heart rate monitors
- Personnel radiation armband wearing management
- Monitoring and management of monthly radiation exposure
- Establish non-ionizing radiation measurement results in each sites
- The process machines reviewing for Non-Ionizing Radiation Related machines
- Manufacturing engineering equipment with labeling management settings
- Semi-annual management of non-independent radiation monitoring
Results
- No instances either verified or suspected instances of radiation exposure.
- Personnel radiation education and training completion rate 100%.
- Results of Monthly Radiation Exposure Monitoring: Normal
- Non-ionizing radiation measurement results of power plants and magnetic fields are far below the ACGIH TLV standard.
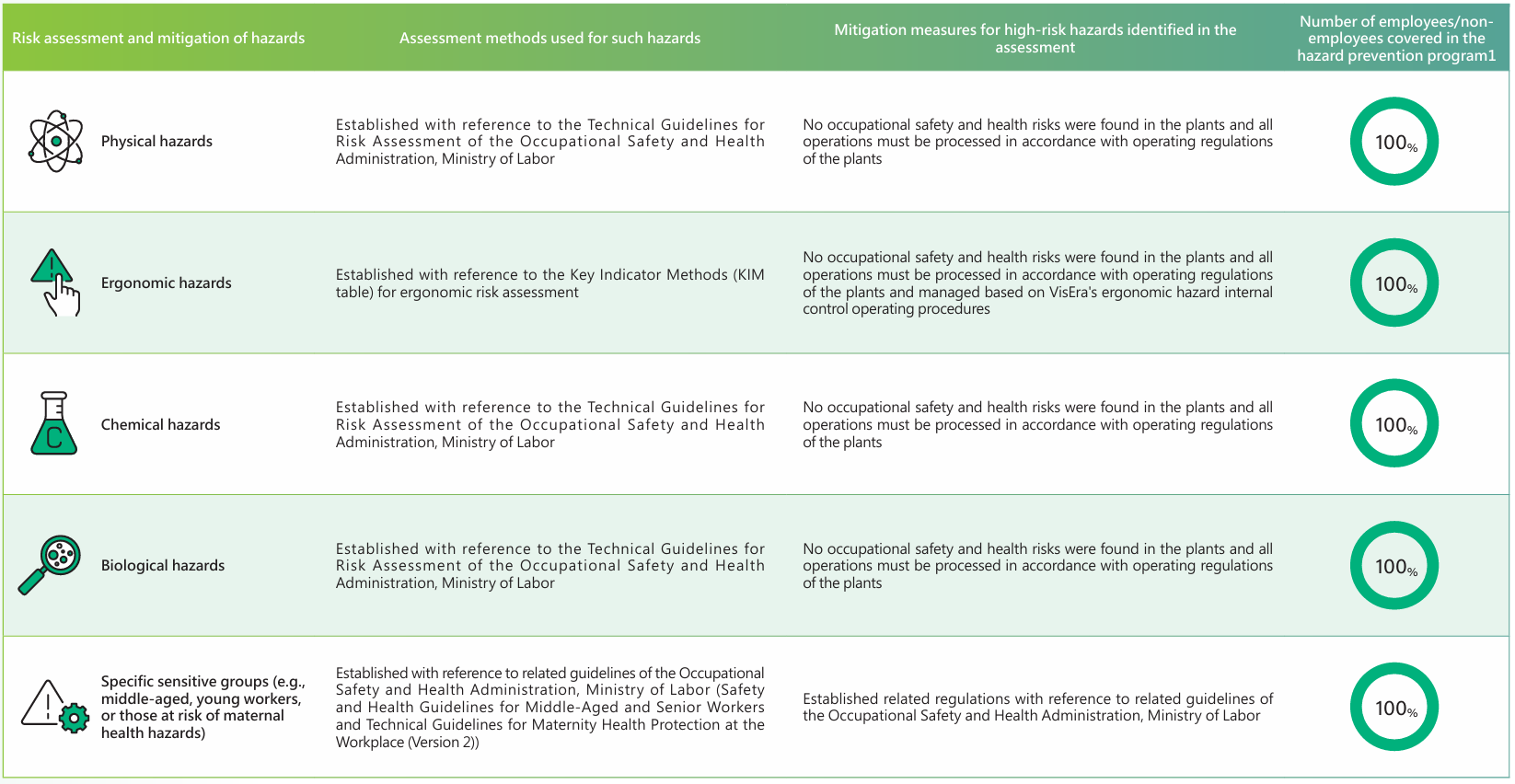
The Company also established accident investigation procedures. In the event of an accident involving an employee or contractor (including anomalies or incidents), investigation procedures are activated to identify the cause of the accident. We aim to clarify the reason to ensure that such accidents do not recur. There were no cases of material, severe, or recordable occupational injuries (including occupational diseases) in 2023.
However, the Company analyzed and reviewed the 2 cases of incindent, 10cases of anomalies and 27 cases of near miss that occurred in 2023* but did not cause specific damages to review the appropriateness of operational risk assessments and ensure continuous and sustained improvements.
* Information Summit Center Taiwan Sites (includes the sites at Hsinchu, Zhongli, and Longtan)
Statistics of occupational safety and health accidents in past years
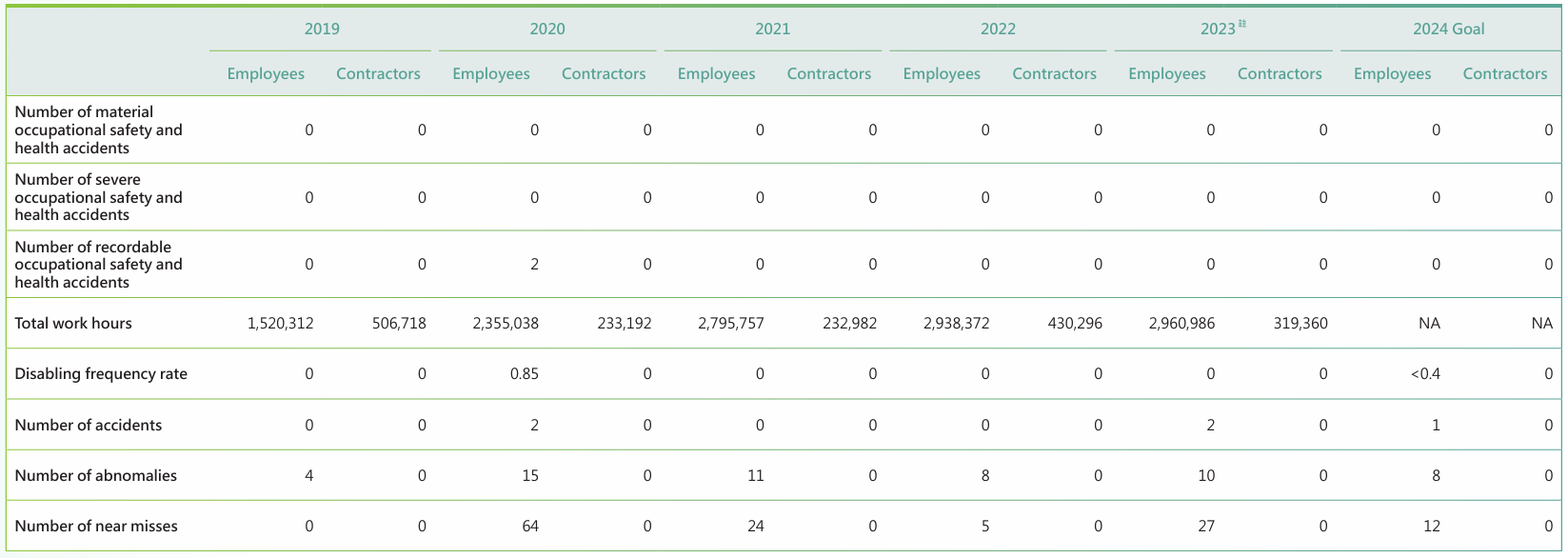
Note:
- Material occupational safety and health accidents: Occupational injuries or occupational diseases that cause death; severe occupational safety and health accidents: Occupational injuries or occupational diseases that necessitate more than 6 months of recovery time (excluding death); recordable occupational safety and health accidents: Occupational injuries or occupational diseases that cause the worker to be unable to perform original functions (including material and severe)
- Disabling frequency rate = number of disabling cases / total work hours *1,000,000
- The disabling injury frequency rate of peers is 0.85 (Information and application platform 113 of the Occupational Safety and Health Management System revealed the overall injury index for each industry throughout the first three years of operation.)
- Accident: It refers to incidents in the workplace that harm equipment or personnel safety and cause injuries or property loss
- Abnomal: It refers to incidents in the workplace that jeopardize the safety of equipment or personnel but have not caused specific injuries or losses
- Near miss: It refers to incidents in the workplace that may jeopardize the safety of equipment or personnel and have not caused specific injuries or losses, but shocked the personnel
- The data from 2019 to 2022 includes Hsinchu site and Zhongli site; the data in 2023 includes Hsinchu site, Zhongli site and Longtan site.
Anomaly analysis
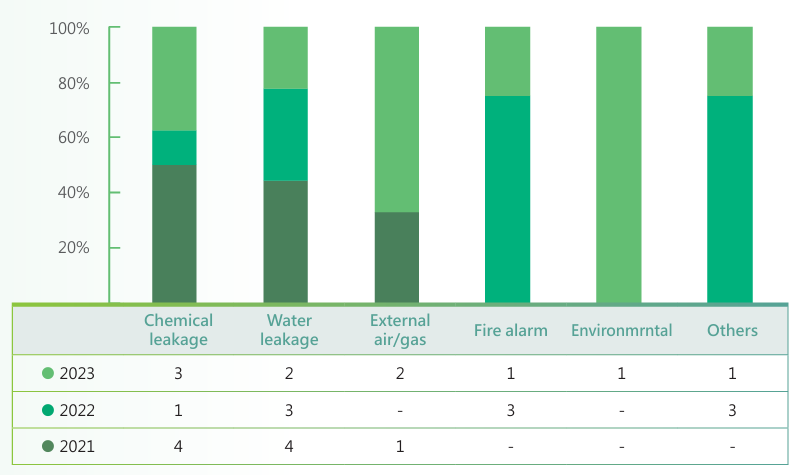
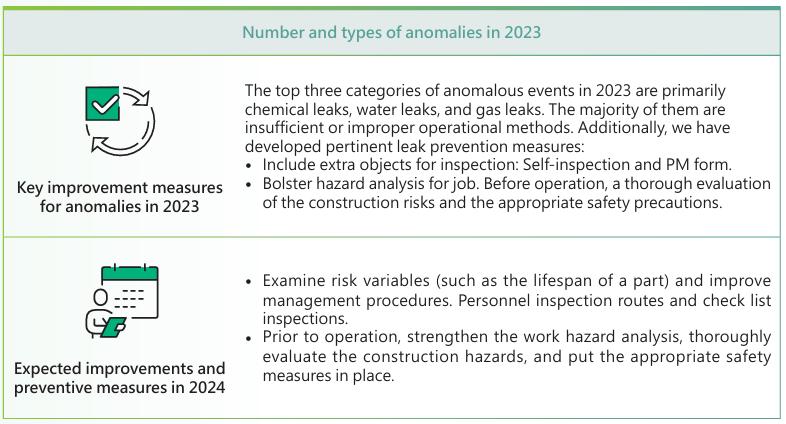
Near miss incident reports and investigation procedures
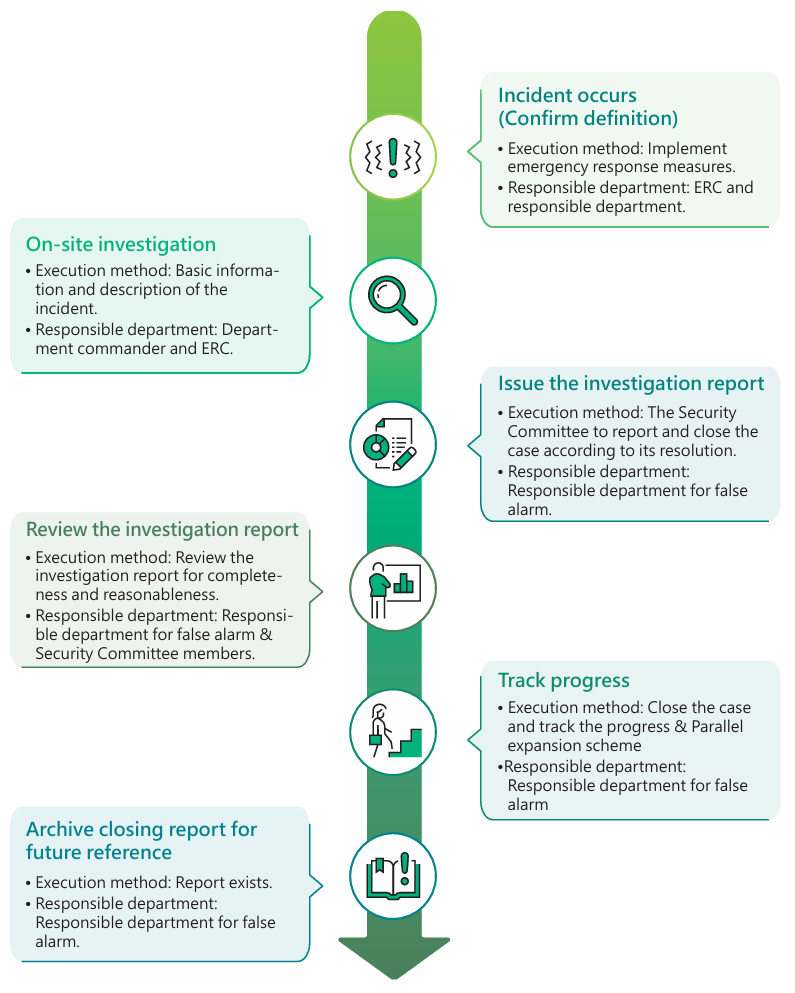
All personnel safety and disaster prevention preparation
VisEra has developed a safety and health training system to enhance the safety and health awareness, responsibility and commitment of all employees, ensure the safety of all employees, and increase the safety awareness of all workers. In addition to the statutory training for all types of operations or business personnel, those who perform ISO 45001 internal audits at the plants are required to receive training as ISO 45001 internal auditors. We also provide safety and health training for contractors. We exercise caution and preparedness to respond to possible accidents. The Company established an emergency response plan and conduct regular or unannounced drills to effectively control and minimize damage of accidents. In 2022, we conducted 38 drills for scenarios including fire, earthquake, gas leak, chemical leak, food poisoning, industrial machinery failure, damage from smoke outside the plant, environmental anomalies, and odor. All drills were conducted in accordance with the regulations and OI (F-RMS-2100 VisEra Emergency Response Plan).
In addition, we organized 18 training sessions (basic, advanced, and commander) for the Emergency Response Team this year and personal protective equipment (PPE) usage tests twice a year. We also assign on-duty personnel on a rotating basis every day to respond to emergencies. If courses are held by means of online courses (V+talent), we conduct evaluations and satisfaction surveys after the courses. If courses are held in person, the instructor engages trainees during the course or the review of test papers to measure the effectiveness of the training. We also conduct a review at the end of the course to enhance the awareness of participants.
Occupational safety and health training and drills in 2023
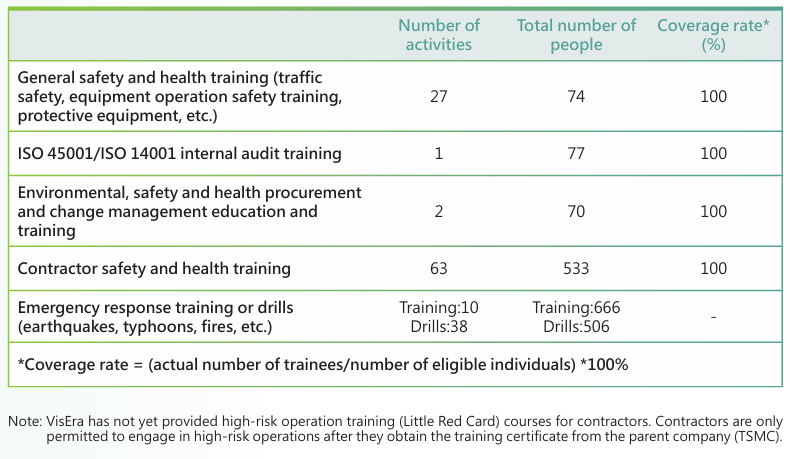
6.4.2 Creating a Comfortable Workplace that Fosters Employees' Physical and Mental Well-being
VisEra adheres to the core value of "Putting People First" and is committed to ensuring the safety and health of its employees. We allocate resources and manpower to create a safe and hygienic work environment, implementing measures such as health risk assessments and environmental monitoring to prevent occupational hazards. We also conduct health check-ups and provide systematic health management information and health promotion activities to enhance the safety and well-being of our employees.
Occupational Health Management
Assessment, monitoring, and mitigation measures related to occupational health management and health hazards in the factory area.
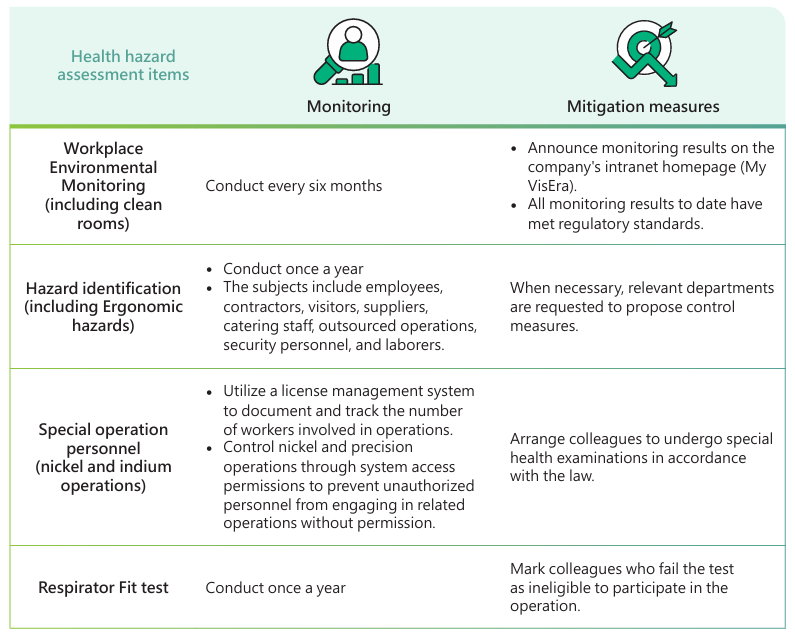
Provide health check-up benefits that are better than regulation.
On-site health consultation assistance is provided with one occupational physician and two general physicians scheduled to be present at the factory for consultations each month (3 hours per physician per month). The services provided include:
- Conduct relevant hazard assessments and provide recommendations based on the requirements of the occupational safety unit.
- Provide consultation, assessment, and recommendations for abnormal personnel conditions, such as special health examination grading management consultation assessment, Ergonomic hazards, abnormalities detected during physical and health examination, and abnormal physiological assessments for respiratory protection.
- Suggestions proposed by on-site physicians will be evaluated and implemented by relevant units, with assistance provided by the Health Center and on-site physicians as needed.
- Continuously monitor and track the health status of personnel with abnormalities, providing assistance in improving health conditions or recommending job suitability adjustments in collaboration with on-site physicians.
In addition, VisEra provides health examination benefits that are better than regulation and implements graded management based on the results of health examinations. For special operation graded management, it follows the Regulations of the Labor Health Protection. In 2023, a total of 423 individuals completed special health examinations, identifying 167 cases with a high potential risk of work-related diseases. General operation graded management is conducted based on the recommendations of on-site physicians, categorizing employees into four levels: normal, mild abnormality, moderate abnormality, and severe abnormality, following the rule of the Regulations of the Labor Health Protection. In 2023, 1,055 individuals participated in health examinations, with 53.45% of employees with moderate to severe abnormal health examination results being regularly monitored.
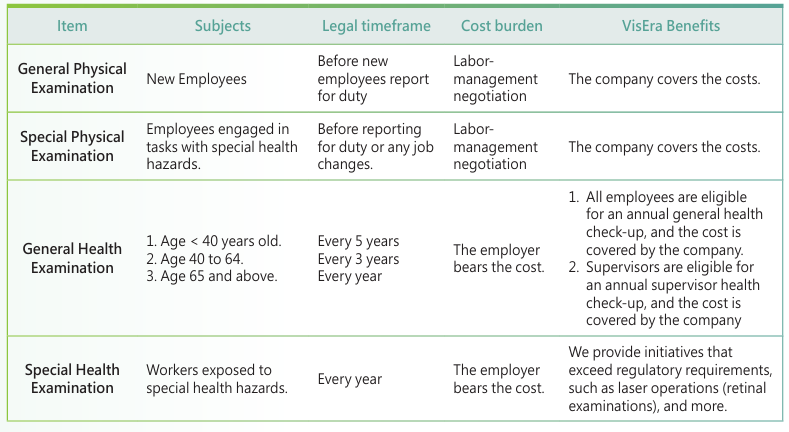
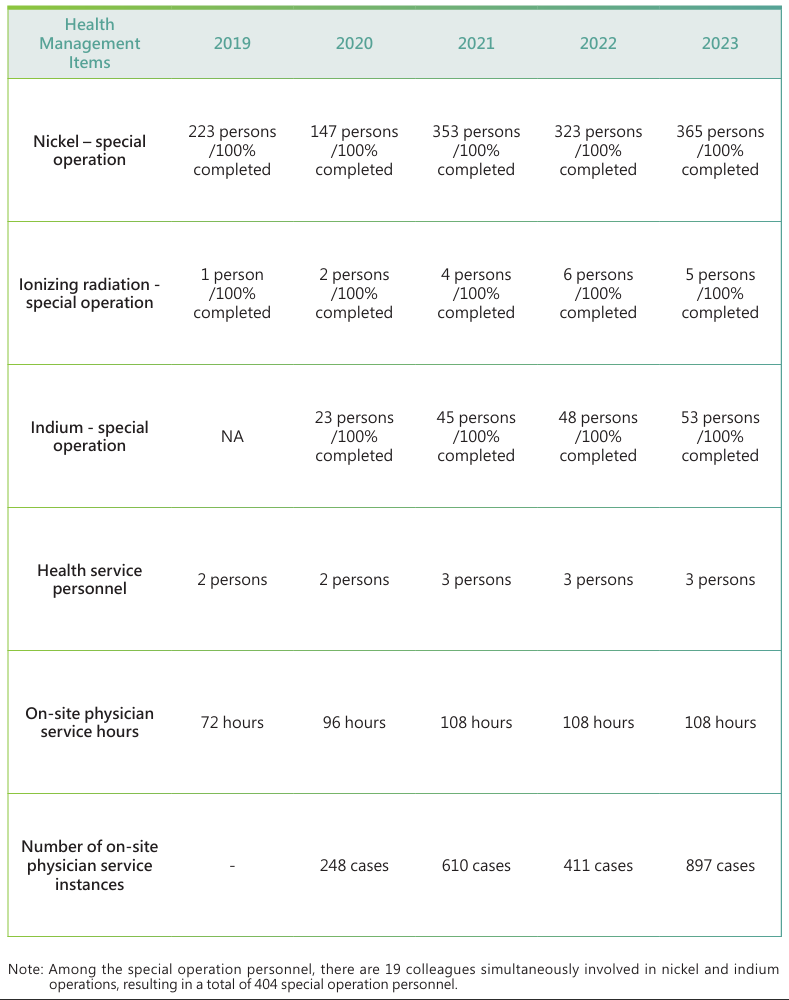
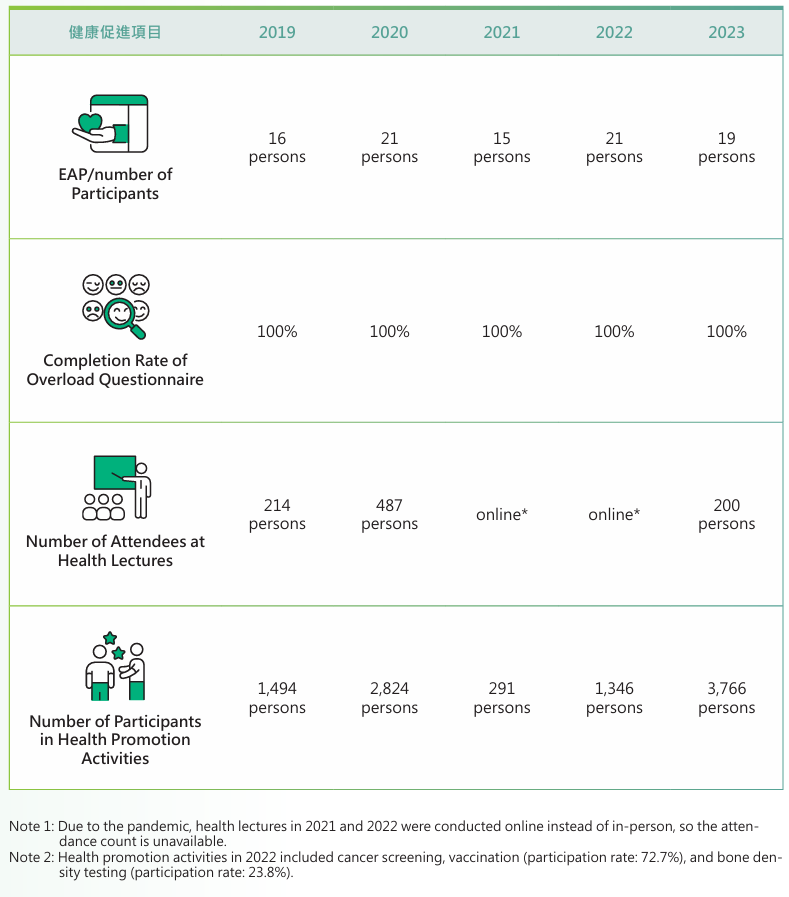
6.4.3 Work with Contractor Partners to Create an Inclusive Workplace
VisEra actively communicates and cooperates with customers and suppliers to jointly improve the safety and health performance of the supply chain. We also share safety and health knowledge and experience with external parties and build partnerships with business partners, industries, governments, academia, and the entire society to build a safe and healthy workplace environment together.
The Blue Book for Contractors' Safety, Health and Environmental Protection was published in 2021 for contractors to enhance their environmental, safety, and health management awareness in all construction operations. Before contractors enter the plant, they must use the construction management system to organize pre-construction safety meetings, construction permit reviews, and completion of safety and health training for all contractor personnel before the access control system permits their entry and implements management and control.
Enhancement of assistance for contractors
We encourage high-risk contractors to obtain ISO 45001 occupational health and safety management system certification. In 2023, 13 contractors responsible for onsite high-risk operations obtained certification (approximately 87%), and we aim to attain 100% certification by 2030. Contractors are not permitted to perform high-risk operations in plant areas without obtaining comprehensive management system certification. We continue to verify the feasibility of JSA work safety analysis through pre-construction surveys and pre-construction meetings for remaining construction items. We ensure that the contractors have sufficient safety and health enforcement capabilities to complete the contracted work on time in accordance with quality and safety requirements.
We also continue to conduct onsite safety, health, and environmental protection audits for suppliers each year. We require a score of at least 70 and provide support. The contract value is used as the basis for screening and grading for onsite audits. We also require reports on improvements for deficiencies and include them as the criteria for the selection of suppliers and contractors. In 2023, we conducted a total of 12 supplier/contractor audits and identified a 55 deficiencies and recommendations during the audits. There were 45 items related to safety and health, 8 items related to fire safety, and 2 items related to environmental protection, and the completion rate of corrections for deficiencies was 96% (53/55), and continued monitoring will be carried out until the improvement reaches 100% completion.
Contractor training
VisEra organizes annual training for new contractors to inform them of the hazards in accordance with regulations. If a new contractor fails to obtain the certification for the hazard communication training course, the contractor will not be able to apply for the VisEra Qualified Vendor Work Permit and will not be able to apply for permission for related construction projects. If a contractor does not have a contractor's work permit, the Company will prohibit the entry of its personnel when reviewing the qualifications of the contractor personnel for entry into the plant.
Contractor environmental, safety, and health assessment procedures
The Company selects contractors with high risk ratings to conduct self-assessments on safety and health every year. We require all contractors to identify mechanical, material, compliance, and environmental risks for the work contents and propose countermeasures during the negotiation and organization meeting. We also require them to conduct environmental, safety, and health audits for the construction project every day. If there are any deficiencies, they must be immediately addressed to effectively reduce the environmental, safety, and health risks.
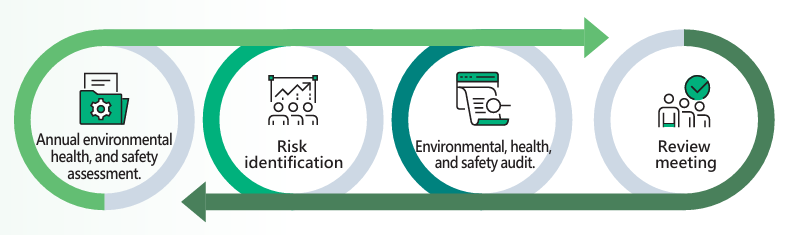
協助承攬商環安衛改善安全衛生投入資源/成本
The Company invests significant amounts of manpower and financial resources each year to increase the safety and health performance of contractors. We reintroduced the contractor safety and health management system in 2023 to improve the efficiency of contractors' construction management procedures in the plants.
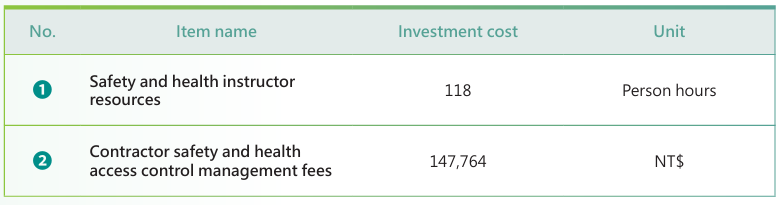
Contractor management and immediate correction
We implement risk-based management for contractors and established the "High-Risk Operation Management Regulations", "High-Risk Area Management Regulations", and "Operation Permit Management Regulations" to require contractors and employees of the Company to work together and ensure safety in construction.
In 2023, we improved the functions of contractor construction management system, and recorded high-risk construction audit results and deficiencies in the electronic system to effectively monitor construction safety issues in the plants. We also implemented 100% high-risk audits so that the Company did not have any occupational accident in 440 high-risk operations and 323,288 hours of contractor operations in the plant in 2023.
These measures are implemented to prevent potential significant casualties of high-risk operations, electric shocks of personnel, fire, leaks of hazardous gases/chemicals, and operations that may cause system shutdown or interrupt production. Contractors are required to apply for work permits for high-risk operations in advance. We also implement restrictions on 14 types of hazardous operations (pipeline operations, roofing operations, installation of bus switches, operations in confined spaces, operations of hazardous machinery, construction scaffolding assembly/dismantling operations at a height of over five meters, LDS cylinder replacement operations for pyrophoric substances, ceiling (including mezzanine) operations, wall removal operations, fire operations, fire sensor isolation, fire safety interruptions, organic solvent operations, and activation of electricity supply panel rated 208V or higher). Supervisors and operators must obtain technical certification (obtain a legal license or the little red card) to be qualified for entering the construction site.
We require contractors to implement the following tasks to promote contractor self-management and implement occupational safety tasks:
- Explain the matters of note for the work of the day, including the operation method, division of labor, safety, and tools and materials used, in the daily toolbox meeting.
- Check the status of the equipment and safety and protection equipment before work.
- Conduct at least three onsite inspections every day. If unsafe conduct or environment is found, they must be addressed immediately and the contractor shall affix his/her signature on the inspection table.
- Supervise onsite operations and oversee personnel at all times.
- Verify the restoration of the environment after operations. If it cannot be immediately restored on the same day, verify whether protection measures are adequate.
The Company's personnel shall implement front-end management with pre-operation reviews such as work permits and independent onsite inspections with the contractor's supervisors. They shall also take measures such as recording violations, deductions, suspension of rights, termination of contract, and request for restoration of damages against the contractor, and impose penalties in accordance with the contract if necessary.
Future safety and health plans
VisEra understands the importance of occupational safety and health for all workers of the Company. We also value and continuously invest resources to create a safe and healthy workplace environment. We planned four major strategies for future improvement with the aim of working with employees and contractors to create a more sustainable work environment.
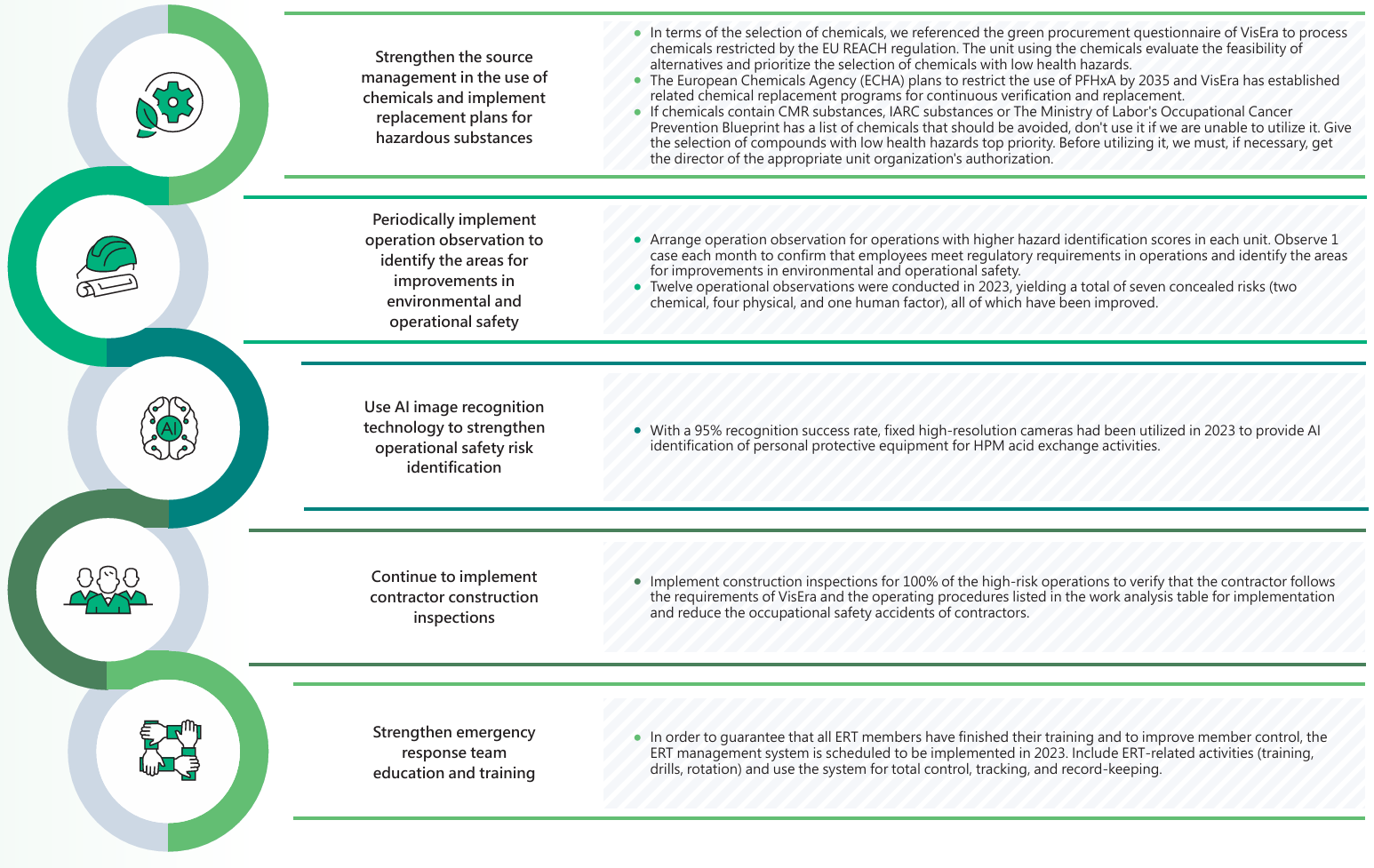
Spotlight
Contractor Management - Engineering vehicle for line-men regulations set up and audits
People are transported to high elevations using engineering vehicle for line-men. The operation process will be impacted if there is a lack of safety management system (safety management is not implemented), unsafe actions by workers during operations, or vehicle body failure, damage, or abnormalities. Accidents could possibly result from potential risks. Thus, the development of a high-altitude work vehicle safety management system will increase managers' managerial skills and assist users in putting safety management into practice to raise operational safety. Therefore, the Occupational Safety and Health Administration of the Ministry of Labor and the Institute of Labor and Occupational Safety and Health have formulated safety management guidelines for the use of high altitude work vehicles, including guidelines for making work plans, automatic inspection technical guidelines and other information references, which can provide users with information to implement independent management and improve work safety.
VisEra has developed pertinent in-factory inspection specifications, including work plan formulation, automatic inspection, operator qualifications, vehicle inspection, and other information, with reference to the guidelines in order to improve the safety of aerial work vehicle operations. The inspection rate in 2023 will be 100%, and the registration will be completed and managed.
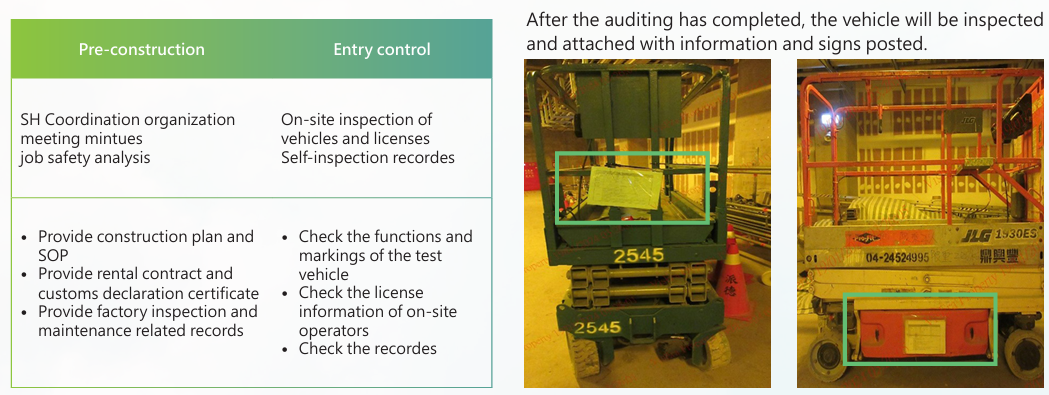